U.S. Air Force and U.S. Navy Accelerate Test Data Analysis
Challenge
Solution
Results
- Two-thirds reduction in development time
- Millions of dollars in projected cost savings
- Immediate, shared access to test results
“We need to identify the cause of an anomaly in test data to determine if we can fly the next day. We don’t have enough time to conduct our analysis with C++. MATLAB helps us get answers immediately because it is quick, easy, and intuitive.”
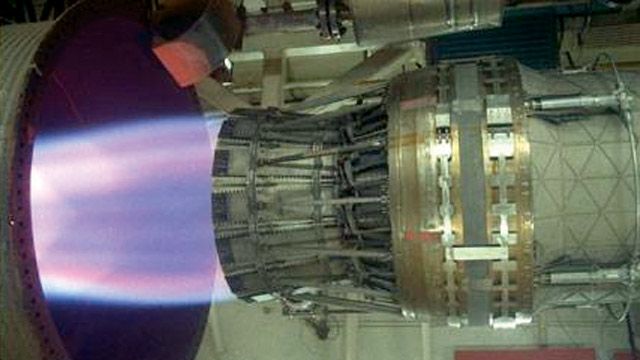
The United States Department of Defense’s (DoD) three major propulsion test centers, Arnold Engineering Development Center (AEDC), the Air Force Flight Test Center (AFFTC), and the Naval Air Systems Command (NAVAIR) Patuxent River site, will save millions of dollars by collaborating on test and evaluation software for the Joint Strike Fighter (JSF) F-35 and other projects.
Responsible for ground-based and in-flight evaluation of propulsion systems, these centers are using MATLAB® as their primary platform for data analysis applications that enable close collaboration among the teams.
“MATLAB provides the Navy and Air Force with an affordable, reliable, sustainable, and technologically superior enterprise-wide approach to test data analysis,” says Dave Kidman, technical expert, Propulsion Integration Branch of the U.S. Air Force.
Challenge
Solution
After an exhaustive review of data analysis software environments and programming languages, the three test centers of the Air Force and Navy standardized on MATLAB for its broad capabilities and widespread adoption in defense organizations and academia.
The test centers have signed a Test Center to Test Center Memorandum of Agreement for developing aero-propulsion post-test data analysis tools based on bat365 products.
“bat365 products helped lay the ground work for this memorandum of agreement,” explains Jeff Corn, Chief of Engineering Projects Section for the U.S. Air Force. “Now, we meet regularly with propulsion groups from the different test centers to assign projects before developing and reusing our analysis work with MATLAB. This approach helps us greatly reduce development time. We’re looking to extend this approach for other types of tests.”
The test centers are using MATLAB and related toolboxes to develop post-flight data analysis tools that are reused across multiple projects, including the F-15, F-16, and JSF F-35.
A propulsion test effort with the F-16 aircraft and the F-110-GE-100 engine involved evaluating engine thrust response. For this effort, the AFFTC team used MATLAB to develop event-detection logic to determine both normal and abnormal engine responses in test data. MATLAB enabled the engineers to accelerate analysis and improve the consistency of results. The AEDC and NAVAIR are modifying and reusing the AFFTC’s analysis work for their own engine thrust analysis testing.
During recent F/A-22 F-119-PW-100 development testing, AFFTC engineers also used MATLAB to calculate inlet recovery and spatial and planar distortion. These tests determine inlet performance and engine-inlet compatibility. The engineers used MATLAB to read data in from hierarchical data format files. They used Signal Processing Toolbox™ to remove noise and extract frequencies from time-series data.
They used MATLAB to store the results in a database for review by flight engineers across test centers. MATLAB also enabled them to create contour plots and videos for visualizing the effects of inlet recovery and turbulence. Using the recovery and turbulence measurements, they assessed air vehicle specification compliance and provided input for flight manuals.
“bat365 products provide the versatility and strength required to develop complex applications without limiting our engineers to one field of research,” notes Cricchi.
Results
Two-thirds reduction in development time. “MATLAB is easier to use and offers many more capabilities than our previous analysis tools,” explains Corn. “With the MATLAB development environment, debugger, profiler, and GUI builder, we can complete development projects in a third of the time.”
Millions of dollars in projected cost savings. “For each test center to independently develop these aero-propulsion analysis tools would cost approximately $15 million over the next five years—approximately $1 million per year per test center. With MATLAB as the common analysis platform, software will be developed once, reducing development costs by up to two-thirds,” explains Kidman.
Immediate, shared access to test results. “Because all the test centers use MATLAB, we can see the same results quickly and work in parallel,” says Corn. “I can now replicate test results immediately, whereas it used to take me a day or more with other tools.”